

All the bobbins will be wound in the same orientation with respect to the black/grey discs. The friction pin is simply to stop the bobbin from free-spinning. Half of them have the friction pin on the black side, and the other half on the grey side. Bobbin frameĮach bobbin has a black and dark grey disc, and a friction pin on one end and an axle on the other. This way it can be loaded up away from the loom if desired, and then clipped in to place. I’ve designed a frame that can hold them all, in the manner of a cartridge. Now each thread can unwind at its own speed, and not be affected by its neighbour. I’ve yet to test that it actually works, but will do in the next few days. My answer to the warp threads running at different speeds has been to make a frame that has 32 individual bobbins one for each thread. The LDraw model for the gearbox can be found at: Bobbin Frame The threads winding on to the thinner areas therefore became slacker, and would get caught on the pinch rollers, ultimately winding back inside them. This meant that the warp drum rotated at the slowest speed, i.e. This was exacerbated by the use of the clutch gear. Now, as the threads wound on, they were winding on at different speeds due to not winding on flat. After watching it load, and thinking on it, it was the same differential speed problem as in the original loom, but in reverse. I was struggling with the threads getting caught up in the pinch rollers as they wound on. This appeared to work well, until the last time I loaded the loom.

When weaving the gearbox would be flipped over to a gear with a friction pin, just to stop the warp drum free-spinning. When engaged, the warp thread drum would rotate at a “surface speed” ever so slightly faster than the feed rate of the pinch rollers – the white clutch gear would deal with any mismatch in speeds. The gearbox would be engaged when loading the warp drum. They would ensure that all the threads passed through the loom at the same speed. The pinch rollers would be in use during weaving, to provide a tension control between the back of the loom and the cloth take-up drum at the front. One of two gearboxes – one either side of the loom to drive the warp thread drum. My solution to the differential winding of the warp drum, was to build a set of pinch rollers, that the warp threads went though, and a gearbox that drove the drum. The LDraw model for this can be found at: Warp Thread Winding Gearbox Due to the different winding thicknesses, this would either result in some threads getting very slack or, more commonly, some threads getting very very tight. When the loom was running it’d pull all the threads through at the same rate. Since the threads didn’t lie completely flat on top of each other, the drum would end up with different “thicknesses” of threads, resulting in some threads winding on faster than others – since C = 2πr. This suffered from a) being tedious, and b) the threads would wind on at different rates. In my original build I used to have to wind the warp threads on, en masse, by hand. This was used at the back of the loom and stored the warp threads for feeding in to the loom. This is the original warp thread winding drum. Warp Thread Drum 3D render of the old warp drum So, without further ado, here are the parts I’ve done so far. I’ll still need to model the main framework of it, but that will come in time.
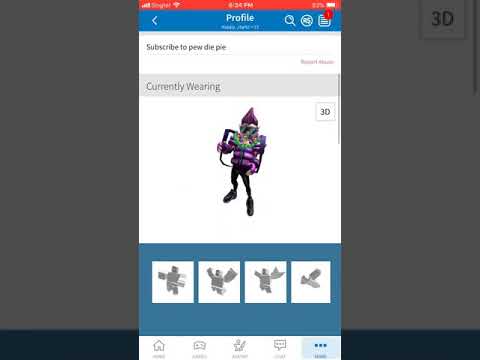

As time goes by I intend modelling the separate “modules” of the loom, and then build up a body of work of all the sections. This way I have the old parts for reference should I ever want to look back on them in the future, and the new parts have been modelled from the start. What I decided to do as I went along was to actually model the parts I was removing, and to model the new parts as I went. Recently I’ve been making changes to the loom, so have been removing old parts and making new modules to replace them. I’ve always said that I’d make them, and I will stick to that … but it’s a BIG task, and will take a long time. Ever since I started to show my LEGO® loom on this blog, Facebook and YouTube, I’ve had people ask me for build instructions.
